Will Anyone Fill The Restored Manufacturing Jobs Trump Promised?
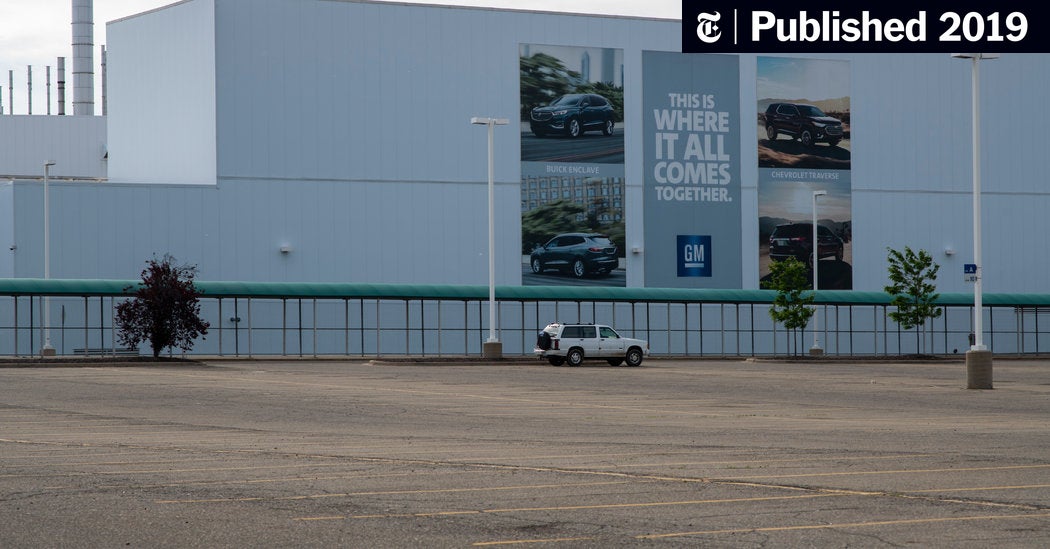
Table of Contents
The Promise vs. the Reality: Assessing Job Growth in Manufacturing
The narrative surrounding restored manufacturing jobs often overshadows the nuanced reality. While the manufacturing sector has experienced some job growth since 2016, it hasn't approached the scale promised during the campaign. A closer look reveals a mixed bag of successes and failures, dependent on various factors.
- Statistics on manufacturing job creation/loss: Official government data reveals a fluctuating pattern of job creation and loss within the manufacturing sector. While certain sub-sectors have seen robust growth, others have experienced significant declines. The net gain, while positive in certain periods, falls short of the ambitious targets initially set.
- Sectors experiencing growth vs. decline: The growth hasn't been uniform across the board. Advanced manufacturing, particularly in areas like pharmaceuticals and technology, has experienced significant growth. Conversely, traditional manufacturing sectors reliant on less skilled labor have struggled to compete globally and have seen job losses.
- Geographic distribution of job growth: Job growth in manufacturing is geographically concentrated. Specific regions with a robust technological infrastructure and a skilled workforce have seen significant gains, while others continue to lag behind. This uneven distribution highlights the need for targeted regional development strategies.
- Impact of trade policies on manufacturing jobs: Trade policies implemented since 2016 have had a complex and often unpredictable impact on manufacturing employment. While some sectors benefited from protectionist measures, others faced challenges due to retaliatory tariffs and disruptions to global supply chains.
The Skills Gap: A Critical Bottleneck in Manufacturing's Revival
The biggest obstacle to fully realizing the potential for restored manufacturing jobs is the persistent skills gap. The manufacturing sector is evolving rapidly, demanding a workforce equipped with advanced technical skills that many current workers lack. This skills gap presents a critical bottleneck, preventing companies from expanding and filling open positions.
- Analysis of needed skills vs. available skills: There's a significant mismatch between the skills required by modern manufacturing and the skills possessed by the available workforce. The demand for workers proficient in advanced automation, robotics, data analytics, and programming far outstrips the supply.
- Impact of automation on required skillsets: Automation is reshaping the manufacturing landscape, demanding a workforce capable of operating, maintaining, and programming sophisticated machinery. This shift requires significant retraining and upskilling initiatives to adapt the existing workforce to the new realities of automated manufacturing.
- Challenges in training and upskilling the workforce: Addressing this skills gap requires substantial investment in training and educational programs. However, challenges include funding limitations, a lack of accessible programs, and the difficulty in attracting younger generations to manufacturing careers.
- The role of education and vocational training programs: Robust vocational training programs and partnerships between educational institutions and manufacturers are crucial to bridging the skills gap. These initiatives must focus on providing hands-on experience, emphasizing advanced technological skills, and fostering a pipeline of skilled workers for the future.
Automation's Double-Edged Sword: Job Displacement and New Opportunities
Automation in manufacturing is a double-edged sword. While it can lead to job displacement in some areas, it also creates new opportunities for skilled workers. The key lies in adapting the workforce to this technological transformation.
- Examples of automated manufacturing processes: Robots are increasingly used in assembly lines, while advanced software controls and monitors complex processes. These advancements improve efficiency and productivity but demand workers with the skills to manage and maintain these systems.
- The demand for skilled workers to operate and maintain automation systems: The increasing complexity of automated systems necessitates a workforce proficient in programming, troubleshooting, and maintaining these technologies. This creates a high demand for skilled technicians and engineers.
- The need for retraining and reskilling initiatives: Retraining programs are critical to equip existing workers with the skills needed for the new automated environment. These programs must be readily accessible, affordable, and tailored to the specific needs of the manufacturing industry.
Attracting and Retaining Skilled Manufacturing Workers: Addressing the Labor Shortage
Attracting and retaining skilled workers requires a multi-pronged approach that addresses the image of manufacturing careers and provides attractive employment packages. This is crucial for effectively filling restored manufacturing jobs.
- Strategies to improve the image of manufacturing careers: Many young people are unaware of the diverse and high-tech nature of modern manufacturing. Targeted marketing campaigns and outreach programs can improve the perception of manufacturing careers.
- Incentives to attract and retain skilled workers: Competitive wages, benefits packages, and opportunities for career advancement are essential for attracting and retaining skilled workers. This includes providing opportunities for professional development and ongoing training.
- The role of government policies and industry partnerships: Government policies that support workforce development, provide tax incentives for companies investing in training, and foster partnerships between industry and educational institutions are critical for addressing the labor shortage.
Conclusion
While some progress has been made in restoring manufacturing jobs, a significant skills gap continues to impede full recovery. The impact of automation demands a proactive approach to workforce development. Addressing the challenge of filling these restored manufacturing jobs requires a collaborative effort. Investing in skills development, promoting compelling manufacturing careers, and embracing technological advancements are vital steps towards building a robust and competitive US manufacturing sector. Let's work together to bridge the skills gap and secure a bright future for American manufacturing. We must find innovative solutions to effectively fill the restored manufacturing jobs and unlock the full potential of this vital industry.
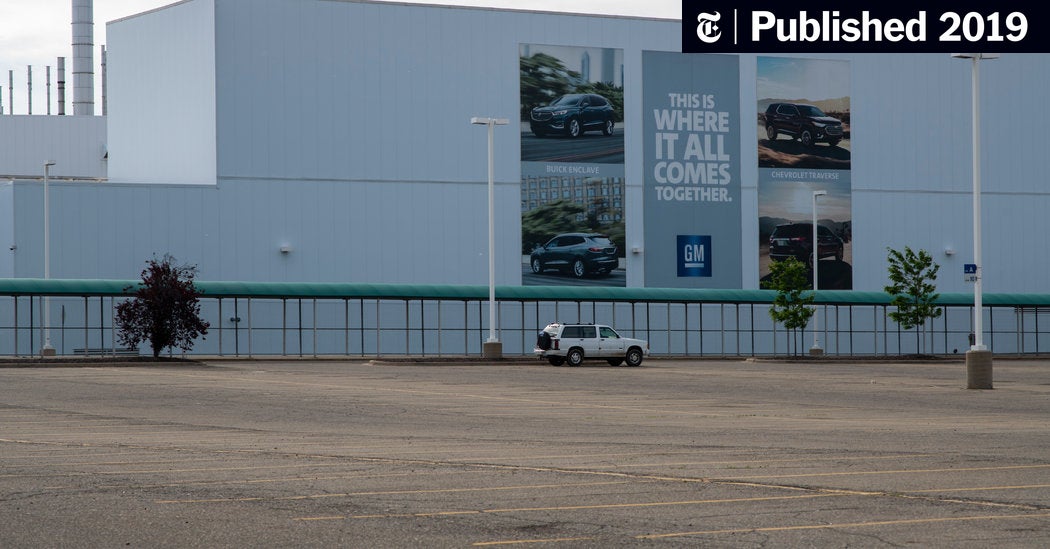
Featured Posts
-
Peppa Pigs Family Celebrates Gender Reveal Party For The Newest Piglet
May 21, 2025 -
Freepoint Eco Systems Announces Ing Project Finance Facility
May 21, 2025 -
Provence Hiking Adventure Mountains To The Mediterranean Coast
May 21, 2025 -
No Es El Arandano Descubre El Superalimento Para Un Envejecimiento Saludable
May 21, 2025 -
Federal Investigation Uncovers Massive Office365 Data Breach Millions Lost
May 21, 2025
Latest Posts
-
Kaellman Ja Hoskonen Jaettaevaet Puolalaisen Seuran
May 21, 2025 -
Impact Of Budget Cuts Fremantles Q1 Revenue Down 5 6
May 21, 2025 -
Mainz Henriksen Following In The Footsteps Of Klopp And Tuchel
May 21, 2025 -
Fremantles Q1 Financial Results 5 6 Revenue Decrease Attributed To Reduced Buyer Spending
May 21, 2025 -
Benjamin Kaellman Potentiaali Kehitys Ja Huuhkajien Tulevaisuus
May 21, 2025