The Robotic Manufacturing Hurdles In Nike Sneaker Production
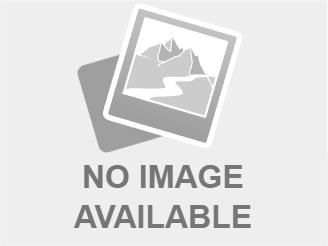
Table of Contents
High Initial Investment Costs and ROI Challenges
The transition to robotic manufacturing requires a substantial upfront investment. This isn't simply about purchasing robots; it encompasses the entire process of integrating them into existing production lines and training personnel to operate and maintain the new systems. The cost of advanced robotics capable of performing intricate tasks like stitching and gluing is exceptionally high. Furthermore, significant expenses are associated with the necessary software, seamless integration with existing infrastructure, and ongoing maintenance. This leads to a lengthy return on investment (ROI) period, potentially delaying profitability and creating uncertainty for Nike's financial planning.
- High cost of advanced robotics specialized for intricate tasks like stitching and gluing. These robots require sophisticated sensors and programming to handle the delicate nature of shoe materials.
- Significant expenses associated with software, integration, and maintenance. Integrating robotic systems into existing production lines often necessitates modifications to the existing infrastructure, adding considerable cost. Ongoing maintenance and software updates are also substantial ongoing expenses.
- Uncertainty regarding long-term ROI due to technological advancements and potential obsolescence. The rapid pace of technological advancement in robotics means that the initial investment could become obsolete relatively quickly, impacting the overall ROI calculation.
A direct comparison between robotic and manual labor costs is complex. While robots can theoretically work 24/7 without breaks or wages, the initial investment and maintenance costs need to be factored into the equation. Calculating a true ROI for robotic manufacturing necessitates a long-term perspective and careful consideration of all associated costs.
Complexity of Sneaker Manufacturing and Adaptability of Robots
Sneaker production is an intricate process involving numerous steps, each demanding precision and dexterity. From cutting and stitching to gluing, assembling, and quality control, the manufacturing process is far from standardized. Adapting robots to handle this complexity presents a significant challenge. Current robotic technology struggles to replicate the flexibility and precision of human hands, particularly when dealing with variations in material consistency and the diverse designs of different shoe models.
- Challenges in replicating the dexterity and adaptability of human hands in handling diverse materials. The various materials used in shoe production (leather, synthetics, fabrics) require different handling techniques, posing a significant hurdle for robotic automation.
- Difficulties in programming robots to manage variations in material consistency and size. Even seemingly minor variations in material thickness or stitching can impact the overall quality of the finished product, requiring sophisticated programming adjustments.
- Need for highly specialized robotic systems for each stage of the production process. The diversity of tasks involved in sneaker manufacturing means that different robotic systems, each with its own specialized programming, are needed for each step of the process.
The limitations of current robotic technology are particularly evident in handling delicate materials and complex assembly steps. This highlights the need for further advancements in robotic dexterity and adaptability before full automation is feasible.
Workforce Displacement and Reskilling Concerns
The implementation of robotic manufacturing inevitably raises concerns about potential job displacement. Addressing the social and economic implications for Nike's workforce is paramount. While automation may boost efficiency, it could also lead to job losses in traditional manufacturing roles. Therefore, proactive reskilling and upskilling programs are essential to transition workers into new roles within the automated factory environment.
- Need for training programs in robotics maintenance, programming, and operation. Creating a skilled workforce capable of maintaining, programming, and operating the new robotic systems is crucial for successful implementation.
- Potential for creating new roles in data analysis, quality control, and system management. Automation generates new roles focused on data analysis to optimize robotic performance, ensuring quality control, and managing the complex robotic systems.
- Importance of addressing employee concerns and anxieties related to job security. Open communication and transparent planning regarding the transition to robotic manufacturing are crucial to alleviate employee anxieties and foster a positive working environment.
The ethical considerations of automation and its impact on employment must be carefully addressed. A thoughtful approach, prioritizing employee well-being and providing opportunities for reskilling, is vital for minimizing negative social and economic impacts.
Integration Challenges and Data Management
Integrating robotic systems into existing production lines is a major challenge. It requires significant modifications and adjustments to existing infrastructure and software. This integration process is complex and demands careful planning and execution. Furthermore, managing the vast amounts of data generated by robotic systems is critical for optimizing performance. Robust data management systems are essential for monitoring robot efficiency, identifying potential problems, and improving overall productivity.
- Difficulty in seamlessly integrating robots with legacy equipment and software. Older equipment and software may not be compatible with modern robotic systems, requiring significant upgrades or replacements.
- Need for effective data collection and analysis to monitor robot efficiency and productivity. Data from robotic systems needs to be collected, analyzed, and used to optimize processes and identify areas for improvement.
- Challenges in dealing with unexpected downtime and troubleshooting robotic malfunctions. Robots, like any complex machinery, are subject to malfunctions. Efficient troubleshooting and repair procedures are crucial to minimize downtime.
Effective data analysis is crucial for improving efficiency and reducing downtime. By analyzing data generated by the robotic systems, Nike can identify areas for improvement, optimize processes, and prevent future issues.
Conclusion
Nike's journey towards fully automated sneaker production faces significant hurdles, encompassing substantial financial investments, the complexity of sneaker manufacturing, workforce transition challenges, and integration difficulties. Overcoming these obstacles requires careful planning, substantial investment in technology and training, and a strategic approach to integrating robotic systems into existing production lines. While the full realization of robotic manufacturing in Nike's factories may still be some time away, ongoing research and development are critical to successfully addressing these challenges and realizing the potential benefits of increased efficiency and production. Further research into overcoming the hurdles of robotic manufacturing is crucial for Nike's future.
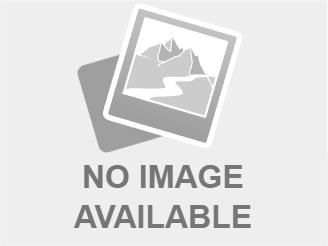
Featured Posts
-
South Sudan And The Us Joint Efforts For Deportees Return
Apr 22, 2025 -
Selling Sunset Star Accuses Landlords Of Price Gouging After La Fires
Apr 22, 2025 -
Open Ais Chat Gpt Faces Ftc Probe What It Means
Apr 22, 2025 -
U S China Relations Breakdown Tensions And The Specter Of A New Cold War
Apr 22, 2025 -
Understanding The Dynamics Of The Countrys Emerging Business Hubs
Apr 22, 2025