Strategies For Effective Automated Visual Inspection Of Lyophilized Vials
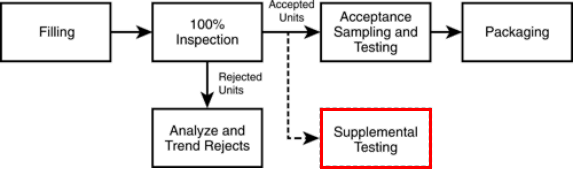
Table of Contents
Selecting the Right Automated Visual Inspection System
Choosing the appropriate automated visual inspection system is the cornerstone of a successful quality control strategy for lyophilized vials. This involves careful consideration of several key factors.
Types of Automated Inspection Technologies
Several technologies are available for automated vial inspection, each with its strengths and weaknesses:
-
Computer Vision Systems: These systems utilize sophisticated algorithms to analyze digital images of vials, identifying defects based on pre-programmed criteria. They offer a good balance of cost and performance, making them suitable for many applications. Examples include systems from Cognex.
-
Machine Vision Systems: Often incorporating more advanced image processing techniques than computer vision, machine vision systems provide higher accuracy and can handle more complex defect detection tasks. Keyence is a prominent manufacturer in this space.
-
AI-Powered Inspection: Artificial intelligence and machine learning algorithms are increasingly used in automated visual inspection. AI systems can learn to identify defects from large datasets, adapting to variations in vial appearance and improving accuracy over time. This adaptability is crucial for handling the inherent variability in lyophilized products.
-
3D Imaging Systems: For complex defects or situations requiring a thorough inspection of the vial's three-dimensional structure, 3D imaging systems offer unmatched precision. These systems, however, tend to be more expensive and slower than 2D systems.
The selection process must also account for:
- Throughput Requirements: The system must be capable of handling the required production volume without creating bottlenecks.
- Vial Size and Shape Variations: The system needs to accommodate variations in vial size, shape, and finish.
- Defect Detection Sensitivity: The system must be sensitive enough to detect even subtle defects while minimizing false positives.
System Integration and Validation
Seamless integration with existing production lines is crucial. The automated visual inspection system must be compatible with existing equipment and processes to ensure smooth workflow. This is particularly important for achieving Good Manufacturing Practices (GMP) compliance. Furthermore, rigorous validation is essential:
- IQ (Installation Qualification): Verifying that the system is correctly installed and configured.
- OQ (Operational Qualification): Demonstrating that the system performs as intended under normal operating conditions.
- PQ (Performance Qualification): Confirming that the system consistently meets predefined performance criteria.
This validation process ensures accuracy and reliability and demonstrates compliance with regulations such as FDA 21 CFR Part 11, which mandates electronic records and signatures for pharmaceutical manufacturing. Selecting a system with robust data management and reporting capabilities is also critical for traceability and compliance.
Optimizing the Inspection Process for Lyophilized Vials
Optimizing the inspection process itself is vital for achieving high accuracy and efficiency in detecting defects in lyophilized vials.
Illumination and Image Acquisition
Proper illumination is crucial for maximizing defect visibility. Different lighting techniques can be employed:
- Coaxial Illumination: Provides even illumination, minimizing shadows and reflections.
- Diffuse Illumination: Reduces specular reflections from the vial surface.
High-resolution cameras and appropriate image capture settings are also critical for capturing clear, detailed images of the vials. The camera resolution and settings must be tailored to the specific vial type and the size of the defects being targeted.
Defect Detection Algorithms and AI
Advanced algorithms play a central role in identifying defects. These algorithms analyze the acquired images, identifying deviations from pre-defined acceptable standards.
- Image Processing Techniques: Algorithms such as edge detection, thresholding, and filtering are used to enhance image quality and highlight potential defects.
- Pattern Recognition: Algorithms identify patterns associated with specific defects, like cracks, particulate matter, or incomplete lyophilization.
- AI and Machine Learning: AI-powered systems can learn to identify defects from large datasets, continually improving their accuracy and reducing false positives. Training the AI model with a representative dataset is crucial for achieving reliable results.
The specific defects targeted should be carefully considered during system setup and algorithm development. Common defects in lyophilized vials include:
- Cracks in the vial
- Particulate matter within the vial
- Incomplete lyophilization (resulting in visible moisture or inconsistencies)
- Scratches or other damage to the vial surface
Handling and Presentation of Vials
Efficient and gentle handling of the vials is essential to prevent damage and maintain image quality. Different vial feeding systems exist:
- Vibratory Bowl Feeders: Simple and cost-effective for many applications.
- Robotic Arms: Offer more precise and controlled handling, suitable for fragile vials.
The chosen system must ensure consistent vial orientation during the inspection process for optimal image acquisition and defect detection.
Data Analysis and Reporting in Automated Visual Inspection
The data generated by the automated visual inspection system provides valuable insights into the quality of the lyophilization process.
Real-time Monitoring and Alerting
Real-time monitoring of the inspection process enables prompt identification and resolution of potential issues. Automated alerts should be implemented to flag out-of-specification results, enabling immediate corrective action.
Data Analysis and Trend Identification
Detailed data analysis reveals trends in defect rates, allowing for proactive improvements in the lyophilization process. This analysis often incorporates statistical process control (SPC) charts to monitor process stability. Data analysis also ensures complete traceability and facilitates audit trails, crucial for regulatory compliance.
Conclusion
Automated visual inspection is no longer optional but a critical component of modern pharmaceutical manufacturing for ensuring the quality and safety of lyophilized vials. By carefully selecting the right system, optimizing the inspection process, and effectively analyzing the resulting data, pharmaceutical manufacturers can significantly improve efficiency, reduce risks, and enhance product quality. Implementing effective strategies for automated visual inspection of lyophilized vials is key to meeting regulatory compliance and delivering high-quality medications to patients. Invest in the right technologies and strategies to ensure the integrity of your products – explore the different options for automated visual inspection systems today to optimize your lyophilization process and benefit from improved quality control and increased efficiency.
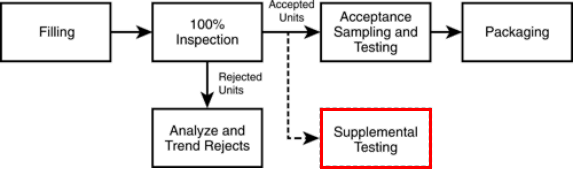
Featured Posts
-
Stevensons Gaze Turns To Next Season Ipswich Town News
May 11, 2025 -
Wiggins Reveals Post Cycling Life Addiction Financial Ruin And The Road To Recovery
May 11, 2025 -
Aaron Judge Ties Babe Ruths Yankees Record A Historic Feat
May 11, 2025 -
Chantal Ladesou Biographie Carriere Et Spectacles
May 11, 2025 -
How Adam Sandlers Netflix Films Led Him To His Wife
May 11, 2025