Overcoming The Difficulties Of Robotic Nike Shoe Manufacturing
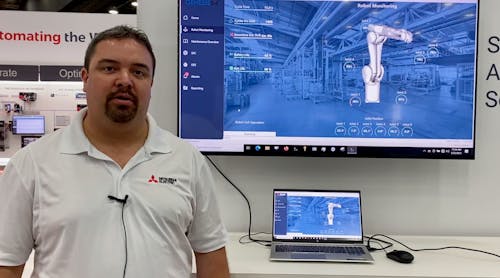
Table of Contents
The Complexity of Shoe Design and Material Handling
Nike shoes are renowned for their intricate designs and the diverse range of materials used in their construction. From supple leather and breathable mesh to durable synthetics, the variety presents a significant challenge for robotic shoe manufacturing. Automating the handling of these materials, each with varying flexibility, texture, and thickness, requires sophisticated robotic systems capable of delicate manipulation. The precision needed is extraordinary.
- Precise material cutting and placement requirements: Achieving millimetre-perfect cuts and placement of materials is crucial for the aesthetic appeal and structural integrity of the finished product.
- Variations in material thickness and density: Robots need to adapt their grip and cutting force to accommodate differences in material properties, preventing damage to delicate fabrics or inaccurate cuts.
- Handling delicate materials without damage: The automated handling of lightweight, easily damaged materials like mesh or thin leather requires gentle manipulation and advanced sensor technology.
- Integration of different robotic systems for diverse tasks: Shoe manufacturing involves a multitude of tasks – cutting, stitching, gluing, assembling – requiring the seamless integration of multiple robotic systems. This integration itself presents a complex engineering challenge.
Successfully addressing these challenges requires advancements in material handling robotics and the development of flexible automation solutions specifically tailored to the nuances of Nike shoe design and material diversity.
Programming and Precision of Robotic Systems
Programming robots to perform the intricate tasks involved in shoe assembly is a major hurdle. The level of robotic precision demanded is exceptionally high. Each stitch, each gluing operation, needs to be executed with pinpoint accuracy and consistent repeatability. Furthermore, incorporating robust error detection and error correction mechanisms is vital to maintain quality control and prevent faulty products.
- Fine motor skills needed for complex assembly: Many aspects of shoe assembly require dexterity and fine motor control, replicating the skill of a human hand.
- Calibration and maintenance of robotic systems: Consistent calibration and regular maintenance are essential for upholding the precision and accuracy of robotic movements.
- Software development for complex tasks: Developing sophisticated software capable of controlling the intricate movements and operations of multiple robotic systems is a complex undertaking.
- Integration of vision systems for quality control: Advanced vision systems are needed to inspect the finished product, ensuring that it meets the high quality standards expected of Nike.
The development of more sophisticated vision systems and advanced programming robots is crucial for addressing the challenges of automated assembly and achieving optimal robotic precision.
Cost and Return on Investment (ROI) of Robotic Systems
The initial investment required for robotic shoe manufacturing is substantial. The cost of purchasing, installing, and integrating advanced robotic systems, along with the necessary infrastructure and skilled personnel, is a significant barrier to entry for many manufacturers. However, the potential for long-term cost savings through increased efficiency and reduced labor costs is substantial.
- High initial capital expenditure for robots and infrastructure: This includes the cost of the robots themselves, specialized tooling, and the factory modifications required for robotic integration.
- Ongoing maintenance and repair costs: Regular maintenance and timely repairs are essential to prevent downtime and ensure the continued operation of the robotic systems.
- Training costs for technicians and engineers: Skilled technicians and engineers are needed to operate, maintain, and program the robotic systems. This requires substantial training investment.
- Potential for increased productivity and reduced labor costs: The increased productivity and reduced labor costs resulting from automation offer significant long-term cost savings.
A thorough cost-benefit analysis is essential to assess the robotics ROI and determine the viability of robotic solutions for Nike production costs. Factors such as production volume, maintenance costs, and labor costs all need to be considered.
Adaptability and Scalability of Robotic Solutions
Adapting robotic systems to handle new shoe designs and materials is a continuous challenge. Nike regularly introduces innovative designs and employs new materials, demanding flexibility from its manufacturing processes. Similarly, the ability to scale production up or down to meet fluctuating demands is essential for maintaining competitiveness.
- Adapting to new shoe models and designs: The robotic systems must be easily reprogrammed and reconfigured to accommodate new designs and manufacturing processes.
- Scaling production capacity up or down as needed: A flexible system is needed to meet seasonal demands or changing market conditions without significant capital investment.
- Integration of new technologies and materials: The system should accommodate the integration of new technologies and materials without requiring significant overhauls.
- Modular design for flexibility and adaptability: A modular design allows for easier reconfiguration and upgrading, enhancing flexibility and adaptability.
The development of flexible robotics and scalable automation solutions, particularly modular robots, is crucial for creating truly adaptable and efficient robotic shoe manufacturing processes. This is key to the future of manufacturing in the footwear industry.
The Future of Robotic Nike Shoe Manufacturing
The challenges discussed – the complexity of shoe design, the need for extreme robotic precision, the significant initial investment costs, and the need for adaptable and scalable solutions – highlight the hurdles in achieving fully automated robotic Nike shoe manufacturing. However, ongoing advancements in robotics, particularly in areas like AI-powered programming, advanced sensor technology, and flexible automation, offer promising solutions. These advancements will contribute to higher efficiency and lower costs, ultimately enhancing Nike’s competitiveness in the global footwear market.
Further research and development in robotic shoe manufacturing is crucial to overcome the existing difficulties and unlock the full potential of automation within the footwear industry. We encourage readers to explore related articles and resources to learn more about the advancements being made in this dynamic field. The future of robotic Nike shoe manufacturing, and indeed the footwear industry as a whole, depends on continued innovation and collaboration in this exciting space.
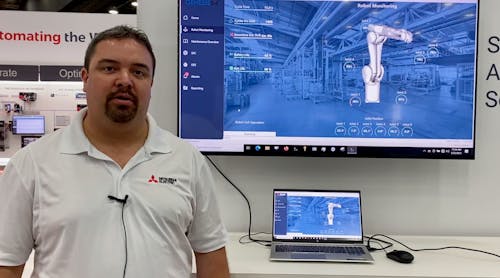
Featured Posts
-
Over The Counter Birth Control Implications For Reproductive Healthcare After Roe V Wade
Apr 22, 2025 -
How Effective Middle Management Drives Company Performance And Employee Satisfaction
Apr 22, 2025 -
Winners And Losers Assessing The Impact Of Trumps Economic Plans
Apr 22, 2025 -
Wga And Sag Aftra Strike The Impact On Hollywood
Apr 22, 2025 -
Pope Francis Legacy A Defining Moment For The Next Conclave
Apr 22, 2025