Optimizing Automated Visual Inspection Systems For Lyophilized Vials
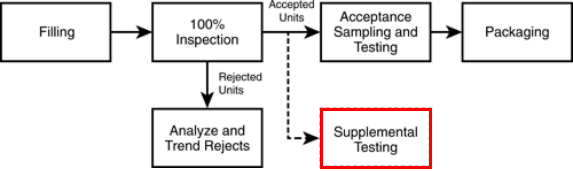
Table of Contents
Selecting the Right Automated Visual Inspection System for Lyophilized Vials
Choosing the appropriate automated inspection equipment is the cornerstone of a successful quality control strategy. Several critical factors influence this selection, impacting both the effectiveness and efficiency of your inspection process. Key considerations include:
-
Resolution and Illumination: High-resolution cameras are crucial for detecting minute defects such as cracks, particulate matter, or inconsistencies in the lyophilized cake. Proper illumination, using techniques like dark-field or bright-field illumination, is essential to maximize contrast and visibility of these imperfections. The system should provide adjustable lighting parameters for optimal visualization depending on the vial type and contents.
-
Image Processing Algorithms: Sophisticated image processing algorithms are the heart of any automated visual inspection system. These algorithms analyze the captured images, identifying deviations from pre-defined quality standards. Look for systems employing advanced algorithms capable of identifying various defects, including:
- Cracks and fissures in the vial or lyophilized cake.
- Particulate matter within the vial.
- Variations in fill level or cake appearance.
- Missing or damaged seals.
- Label inconsistencies.
-
Throughput and Speed: While accuracy is paramount, the system's throughput must also align with your production demands. Higher throughput systems reduce inspection bottlenecks, but ensure that speed doesn't compromise the accuracy of defect detection. Consider the system's capacity and potential scalability to accommodate future production increases.
-
System Integration: Seamless integration with your existing production line and data management systems is critical. The system should easily interface with existing equipment and databases, allowing for efficient data transfer and streamlined workflows. This often involves considerations for communication protocols (e.g., OPC UA, Ethernet/IP) and data formats.
-
Validation and Compliance: Rigorous validation is non-negotiable, particularly within the pharmaceutical industry. The chosen automated visual inspection system must comply with relevant regulatory standards, such as FDA 21 CFR Part 11 and GMP guidelines. Ensure the system provides comprehensive documentation to support validation and compliance activities.
Optimizing Inspection Parameters for Enhanced Defect Detection
Even the most advanced automated visual inspection system requires careful parameter optimization to achieve peak performance. Fine-tuning these parameters significantly impacts the system's sensitivity and specificity, directly influencing the accuracy of defect detection and minimizing false positives.
-
Threshold Settings: Adjusting sensitivity and specificity thresholds is crucial for balancing defect detection with the minimization of false positives. Higher sensitivity may increase the number of detected defects but also increase false positives, while higher specificity reduces false positives but might miss some real defects. Optimization involves finding the balance that maximizes true positive detection while minimizing false positives. This often requires iterative testing and adjustment based on historical data and defect analysis.
-
Lighting and Camera Angles: The angle and type of lighting significantly influence defect visibility. Experimenting with different lighting configurations (e.g., diffuse vs. direct lighting) and camera angles can improve the detection of specific defect types. Consider using multiple light sources and angles to maximize defect visibility from various perspectives.
-
Calibration and Maintenance: Regular calibration and preventative maintenance are critical for maintaining the accuracy and reliability of the automated visual inspection system. A scheduled calibration protocol, using certified standards, ensures consistent performance over time. Regular maintenance helps prevent malfunctions and ensures optimal system performance.
-
Algorithm Training: Many modern systems utilize machine learning algorithms for defect detection. Continuous training of these algorithms with diverse datasets, including images of various defects and non-defective vials, enhances their accuracy and ability to identify new or evolving defect types. This iterative training process ensures the system adapts and improves over time.
Implementing a Robust Quality Control Program for Automated Visual Inspection
A comprehensive quality control program is vital to maximize the benefits of your automated visual inspection system. This program ensures consistent performance, identifies potential issues early, and enables continuous improvement.
-
Data Analysis and Reporting: The system should generate detailed reports on inspection results, including the number and type of defects detected, their location on the vial, and the frequency of occurrence. This data provides valuable insights into potential manufacturing issues and trends. Effective data management and reporting are crucial for trend analysis and continuous improvement efforts.
-
Statistical Process Control (SPC): Implementing SPC techniques allows for continuous monitoring of the system’s performance. Tracking key metrics, such as defect rates and false positive rates, allows for early detection of deviations from acceptable limits, enabling prompt corrective action. Control charts and other SPC tools help identify trends and potential problems before they escalate.
-
Defect Analysis and Root Cause Investigation: When defects are identified, a thorough investigation should be conducted to determine the root cause. This may involve examining manufacturing processes, raw materials, or equipment malfunctions. Root cause analysis helps implement corrective actions to prevent future occurrences of similar defects.
-
Operator Training: Operators responsible for system operation, maintenance, and data analysis require comprehensive training. This training should cover system operation, troubleshooting, preventative maintenance, data interpretation, and compliance procedures. Regular refresher training ensures continued competence and adherence to best practices.
Conclusion
Optimizing automated visual inspection systems for lyophilized vials is crucial for ensuring product quality, patient safety, and regulatory compliance within the pharmaceutical industry. By carefully selecting the right equipment, optimizing inspection parameters, and implementing a robust quality control program, manufacturers can significantly enhance the efficiency and accuracy of their inspection processes. Optimize your automated visual inspection system today to improve your lyophilized vial quality control with advanced inspection technology. Explore solutions for enhanced automated visual inspection of your lyophilized vials and ensure your products meet the highest quality standards.
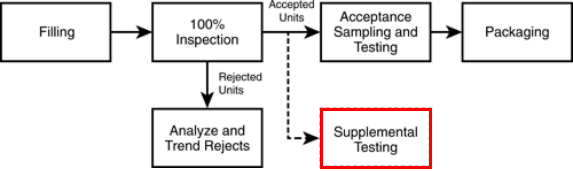
Featured Posts
-
The Rise Of Manon Fiorot One Loss Twelve Wins And A Ufc Career
May 11, 2025 -
The Witchers Sirens Of The Deep Explaining Henry Cavills Non Appearance As Geralt
May 11, 2025 -
New Music From Jessica Simpson Eric Johnsons Support Revealed
May 11, 2025 -
Zurich Classic Mc Ilroy And Lowry Face Steep Climb For Repeat Win
May 11, 2025 -
Comparativa Mejores Billeteras Virtuales Uruguayas Para Argentinos Sin Costo
May 11, 2025