Improving Automated Visual Inspection For Lyophilized Vials
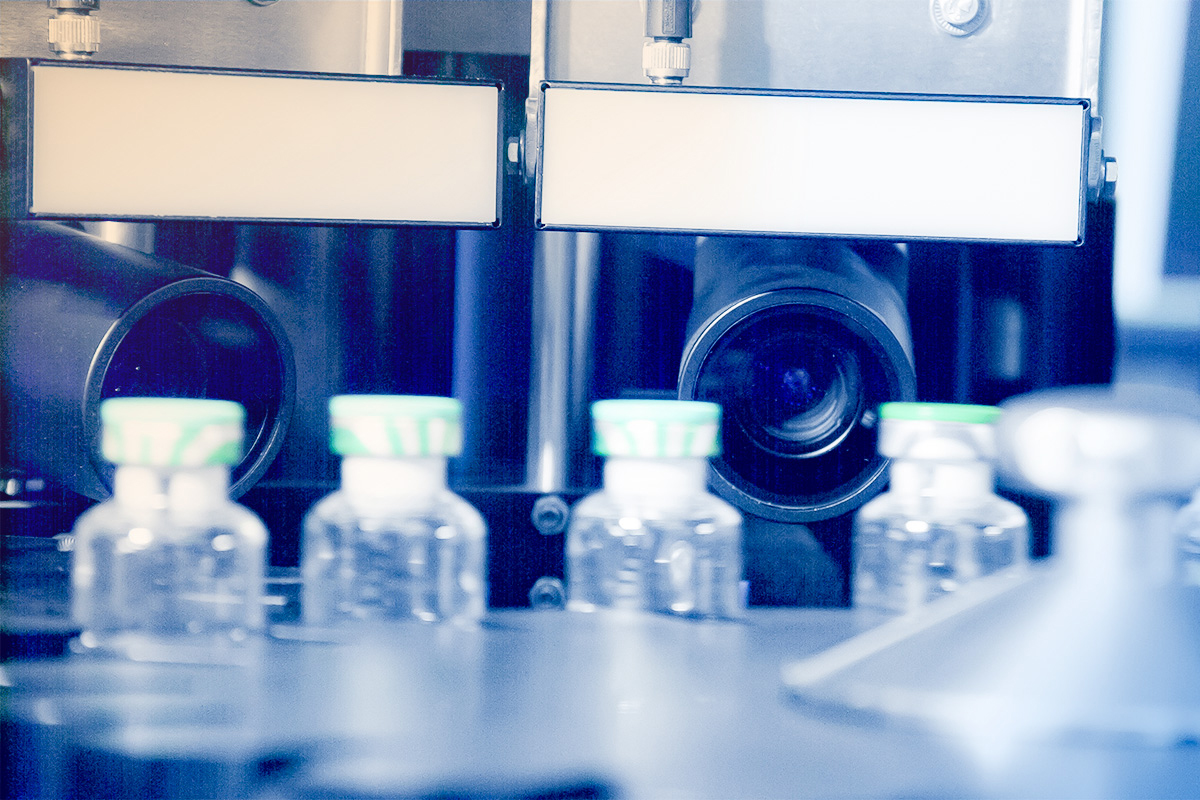
Table of Contents
Enhancing Image Acquisition for Superior Results
High-quality image acquisition is paramount for accurate defect detection in automated visual inspection of lyophilized vials. Poor image quality directly impacts the system's ability to identify critical defects such as particulate matter, cracks, or vial imperfections. This section focuses on optimizing the imaging process for optimal results.
-
High-Resolution Imaging: Utilizing high-resolution cameras is essential for capturing fine details crucial for identifying subtle defects. The higher the resolution, the more precise the image, leading to more accurate defect detection. Consider the resolution needed to detect the smallest acceptable defect size.
-
Consistent Lighting: Consistent and even lighting is critical to minimizing shadows and maximizing contrast. Shadows can obscure defects, leading to false negatives. Various lighting techniques, including coaxial, diffuse, and ring lighting, can be employed to achieve optimal illumination. Careful consideration of light intensity and angle is key to achieving uniform illumination across all vials.
-
Camera Settings Optimization: Proper camera settings are crucial for capturing clear, high-quality images. Optimizing exposure, gain, and focus significantly impacts image quality. Incorrect settings can lead to overexposed or underexposed images, making defect detection difficult. Regular calibration of the camera is essential to maintain consistent image quality over time.
-
Addressing Transparent Vials and Reflections: Lyophilized vials are often transparent, posing challenges for image acquisition due to reflections. Techniques like polarized lighting or specialized filters can help minimize reflections and improve contrast, enabling better visualization of internal defects.
Advanced Image Processing Algorithms for Defect Detection
Sophisticated image processing algorithms are the core of any effective automated visual inspection system. These algorithms analyze the acquired images, identifying deviations from the expected appearance and classifying them as defects. The choice and optimization of these algorithms significantly impact the accuracy and speed of defect detection.
-
Machine Learning and Deep Learning: Machine learning (ML) and deep learning (DL) algorithms are particularly effective in identifying subtle defects that might be missed by traditional methods. These AI-powered algorithms can learn from large datasets of defective and non-defective vials, improving their accuracy over time.
-
Algorithm Training and Validation: Proper training and validation of the algorithms are critical for ensuring their accuracy and reliability. A representative dataset, including a wide range of defects and variations, is needed for effective training. Validation ensures the algorithm performs as expected in real-world scenarios.
-
Distinguishing Critical Defects: Effective algorithms must be able to differentiate between critical defects (e.g., particulate matter, cracks, leaks) and acceptable variations in vial appearance. This requires careful algorithm design and training to establish clear thresholds for defect classification.
-
Computer Vision Techniques: Computer vision techniques, such as edge detection and pattern recognition, are employed to identify various types of defects. These techniques help in analyzing the image characteristics and differentiating them from background noise.
Optimizing the Automated Visual Inspection System Workflow
Optimizing the entire workflow of the automated visual inspection system is crucial for maximizing its efficiency and reliability. This includes aspects ranging from system integration and calibration to handling and data analysis.
-
System Integration: Integrating the automated system seamlessly into the existing production line minimizes disruptions and improves overall efficiency. This may involve conveyor systems, robotic arms, and other automated handling equipment.
-
Calibration and Maintenance: Regular calibration and preventative maintenance are essential for ensuring the accuracy and longevity of the system. This involves checking camera settings, lighting, and algorithm performance.
-
Vial Handling and Presentation: Consistent handling and presentation of vials to the inspection system are critical for accurate image capture. Automated systems should ensure uniform vial positioning and orientation to minimize variations in lighting and imaging conditions.
-
Minimizing False Positives and Negatives: Careful parameter adjustment and algorithm refinement are essential to minimize both false positives (identifying non-defects as defects) and false negatives (missing actual defects). This requires ongoing monitoring and optimization of the system's performance.
Data Analytics and Process Improvement
Data collected from the automated inspection system provides valuable insights into defect trends and areas for improvement. Analyzing this data facilitates proactive quality control and preventative maintenance.
-
Identifying Root Causes: Data analytics can be used to pinpoint recurring defect types and their root causes. This information can be used to identify issues in the manufacturing process, leading to improved quality control measures.
-
Proactive Quality Control: By identifying trends and potential problems early on, manufacturers can implement proactive measures to prevent defects from occurring in the first place. This leads to reduced waste and improved product quality.
-
Key Metric Tracking: Generating reports that track key metrics such as defect rate, inspection speed, and system uptime allows for continuous monitoring and optimization of the system's performance. This data can be used to identify areas needing improvement and to justify further investment in the system.
Regulatory Compliance and Validation
Adherence to regulatory guidelines is crucial for automated visual inspection systems in pharmaceutical manufacturing. This includes validation and documentation to ensure compliance with industry standards.
-
Relevant Regulations: Manufacturers must comply with relevant regulations, such as FDA guidelines (e.g., 21 CFR Part 11) and Good Manufacturing Practices (GMP). These regulations outline requirements for data integrity, system validation, and record-keeping.
-
System Validation: Thorough system validation is necessary to demonstrate that the automated visual inspection system accurately and reliably detects defects. This involves establishing documented procedures and testing to verify the system's performance.
-
Documentation and Record-Keeping: Maintaining comprehensive documentation and records of system performance, calibration, maintenance, and validation is crucial for audits and inspections. This documentation must be readily accessible and auditable to demonstrate compliance.
Conclusion
Improving automated visual inspection for lyophilized vials is crucial for enhancing the quality, efficiency, and regulatory compliance of pharmaceutical manufacturing. By implementing the strategies outlined above—optimizing image acquisition, utilizing advanced image processing algorithms, streamlining the inspection workflow, and leveraging data analytics—manufacturers can significantly improve the accuracy and speed of defect detection. This leads to higher-quality products, reduced costs, and increased confidence in meeting stringent regulatory requirements. Investing in and continually refining your automated visual inspection system will yield significant returns in improving the overall quality of your lyophilized vial production. Don't delay – start improving your automated visual inspection for lyophilized vials today!
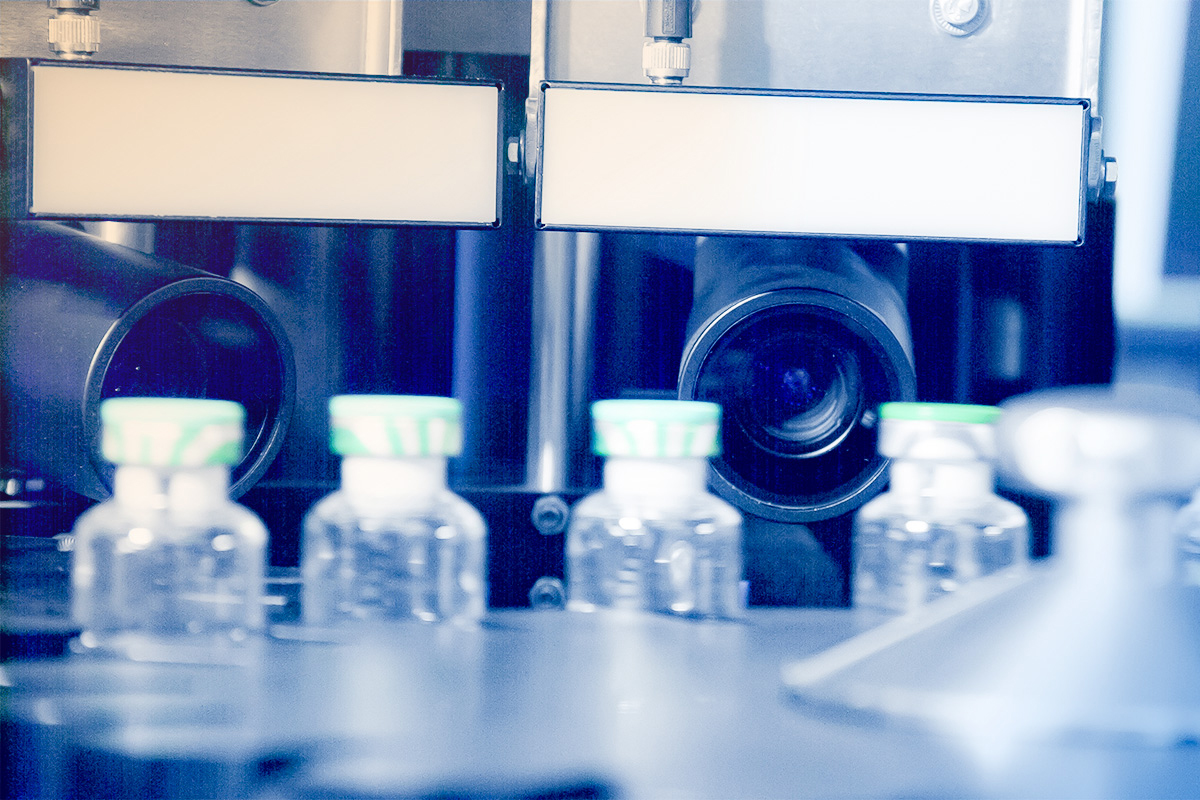
Featured Posts
-
Selena Gomez And Benny Blancos Nsfw Slip Up A Tmi Moment
May 11, 2025 -
Offshore Drilling In Uruguay The Search For Oil And Gas
May 11, 2025 -
Sylvester Stallone Ranks His Rocky Films Which One Touches Him Most
May 11, 2025 -
Celtics Game 1 Win Payton Pritchards Playoff Contribution
May 11, 2025 -
3 Epic Mma Fights To Watch 5 10 And 25 Minute Battles Mma Torch
May 11, 2025