Efficient Automated Visual Inspection: Addressing Challenges In Lyophilized Vial Analysis
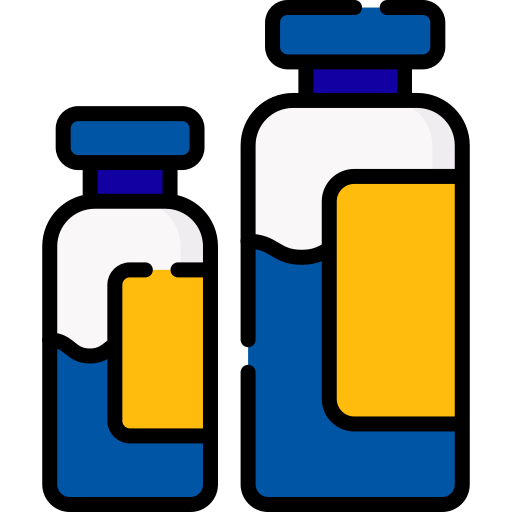
Table of Contents
Challenges in Manual Lyophilized Vial Inspection
Manual inspection of lyophilized vials presents several significant challenges that directly impact product quality, regulatory compliance, and overall production efficiency.
Subjectivity and Variability
Manual visual inspection is inherently subjective. The detection of defects like cracks, particulate matter, or discoloration relies heavily on the individual inspector's judgment. Factors such as lighting conditions, inspector fatigue, and individual interpretation biases contribute to inconsistencies in defect detection.
- Examples of subjective defects: Identifying hairline cracks, differentiating between acceptable and unacceptable levels of particulate matter, assessing the uniformity of the lyophilized cake.
- Impact on product quality and regulatory compliance: Inconsistencies in defect detection can lead to the release of substandard products, increasing the risk of product recalls and regulatory non-compliance.
Time and Cost Inefficiencies
Manual inspection is incredibly time-consuming, especially when dealing with high-volume lyophilized vial production. This significantly impacts throughput and increases labor costs.
- Increased labor costs: The need for a large team of inspectors adds significant expense to the production process.
- Potential for bottlenecks in production lines: Manual inspection often creates bottlenecks, slowing down the entire production process.
- Delayed time-to-market: Delays in inspection can impact the timely release of products, potentially losing market share and revenue.
Risk of Human Error
Human error is an unavoidable factor in manual inspection. Inspectors may miss critical defects, leading to potentially serious consequences.
- Examples of undetected defects: Small cracks, minute particles, or subtle discolorations may easily be overlooked by human inspectors.
- Potential regulatory consequences: Failure to detect and remove defective vials can lead to severe regulatory penalties and reputational damage.
- Financial implications of product recalls: Recalling a batch of lyophilized vials due to undetected defects can be extremely costly.
Benefits of Automated Visual Inspection in Lyophilized Vial Analysis
Automated visual inspection systems offer a compelling solution to the challenges of manual inspection, delivering significant benefits across various aspects of lyophilized vial analysis.
Enhanced Accuracy and Consistency
Automated systems utilize advanced imaging techniques and sophisticated algorithms to achieve superior accuracy and consistency in defect detection.
- Objective defect identification: Automated systems eliminate subjective interpretation, providing objective and consistent defect detection.
- Reduced variability: Automation minimizes the variability inherent in manual inspection, ensuring consistent quality across all batches.
- Improved data traceability: Automated systems generate detailed reports and data logs, providing complete traceability of inspected vials.
Increased Throughput and Efficiency
Automation dramatically increases throughput and efficiency, reducing processing time and labor costs.
- Faster inspection speeds: Automated systems can inspect vials significantly faster than human inspectors, boosting production capacity.
- Increased production capacity: Higher inspection speeds translate to increased production capacity and improved output.
- Reduced labor costs: Automation significantly reduces the need for manual labor, lowering overall production costs.
- Improved ROI: The initial investment in an automated system is quickly recouped through increased efficiency and reduced labor costs.
Improved Data Management and Reporting
Automated visual inspection systems generate comprehensive data logs and reports, simplifying quality control and regulatory compliance.
- Real-time defect tracking: Automated systems provide real-time monitoring of defect rates, allowing for immediate corrective actions.
- Automated data analysis: The system automatically analyzes the collected data, identifying trends and patterns in defect occurrence.
- Simplified regulatory compliance: Detailed reports and data logs facilitate compliance with stringent regulatory requirements.
- Enhanced traceability: Complete traceability ensures that every vial's inspection history is documented and easily accessible.
Key Features of Automated Visual Inspection Systems for Lyophilized Vials
Modern automated visual inspection systems incorporate several key features that are essential for accurate and efficient lyophilized vial analysis.
High-Resolution Imaging
High-resolution imaging is crucial for detecting even the smallest defects in lyophilized vials.
- Examples of defects visible only with high resolution: Microscopic cracks, minute particulate matter, subtle variations in fill level.
- Improved sensitivity for small particles or cracks: High-resolution imaging enhances the sensitivity of the system, ensuring no defects are missed.
Advanced Algorithms and AI
Advanced algorithms and Artificial Intelligence (AI) play a critical role in automated defect recognition and classification.
- Examples of AI-powered defect detection: AI can learn to identify complex defects and patterns, improving accuracy and reducing false positives.
- Improved accuracy in identifying complex defects: AI algorithms can be trained on large datasets of images, increasing their ability to accurately identify complex defects.
Integration with Existing Production Lines
Seamless integration with existing production lines and quality control systems is vital for a smooth implementation.
- Reduced downtime during implementation: Systems designed for easy integration minimize downtime during installation and commissioning.
- Compatibility with different vial sizes and formats: Flexible systems can handle a wide range of vial sizes and formats, avoiding the need for separate equipment.
Conclusion
Efficient automated visual inspection is revolutionizing lyophilized vial analysis, offering significant advantages over traditional manual methods. By addressing the challenges of subjectivity, time constraints, and human error, automated systems ensure enhanced accuracy, consistency, and efficiency in quality control. The improved data management capabilities simplify regulatory compliance, while increased throughput and reduced labor costs contribute to a significant return on investment. To enhance the quality control of your lyophilized vial production process and achieve superior product quality and regulatory compliance, explore the benefits of automated visual inspection systems. Contact a leading provider of automated inspection solutions for lyophilized vials today to learn more about how automation can transform your operations.
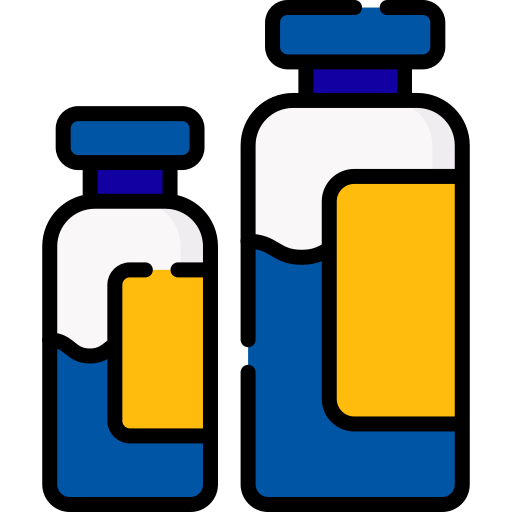
Featured Posts
-
Jessica Simpson And Eric Johnson Spotted Together Amidst Divorce Rumors
May 12, 2025 -
Jamaicas Grand Slam Triumph A Detailed Look
May 12, 2025 -
Who Could Be The Next Pope Leading Candidates And Their Platforms
May 12, 2025 -
Thomas Muellers Last Home Game Bayern Munich Secure Bundesliga
May 12, 2025 -
The Challenge Season 41 Spoiler Alert Unexpected Twist
May 12, 2025
Latest Posts
-
Stallones Favorite Rocky Unveiling The Franchises Most Poignant Chapter
May 12, 2025 -
Which Rocky Movie Touches Stallone The Most The Actor Names His Emotional Favorite
May 12, 2025 -
Rockys Emotional Heart Stallone Reveals His Favorite Film In The Iconic Franchise
May 12, 2025 -
The Forgotten Directing Effort Of Sylvester Stallone A Box Office Bomb
May 12, 2025 -
Sylvester Stallones Underrated Directing Career Focusing On His One Non Acting Film
May 12, 2025