Addressing Challenges In Automated Visual Inspection Of Lyophilized Vials
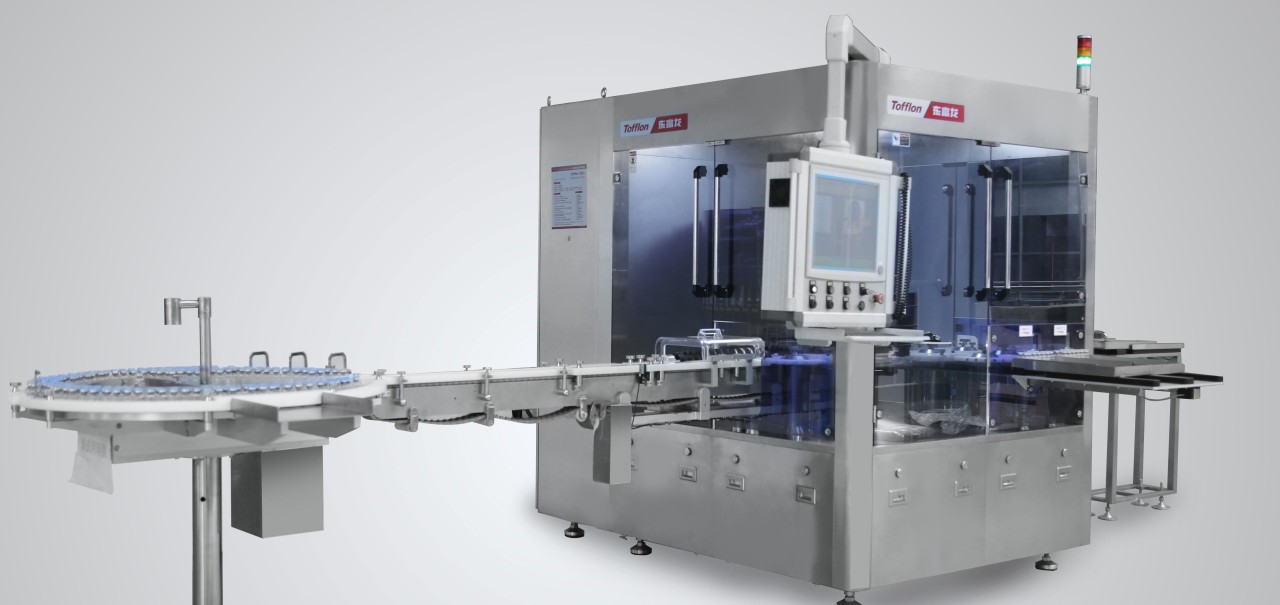
Table of Contents
Image Acquisition and Preprocessing Challenges
Effective automated visual inspection begins with high-quality image acquisition and preprocessing. This stage, however, is fraught with difficulties specific to lyophilized vials.
Lighting and Shadow Effects
Achieving consistent and uniform illumination is paramount. Uneven lighting creates shadows and reflections that can mask critical defects, rendering the inspection process unreliable. The challenge is amplified by:
- Varied Vial Shapes and Orientations: Vials come in various shapes and sizes, making it difficult to achieve uniform lighting across all surfaces.
- Impact of Ambient Light: External light sources can interfere with the controlled lighting setup, introducing inconsistencies.
- Solutions: Specialized lighting systems, such as coaxial lighting, are crucial. These systems illuminate the vial from the same direction as the camera, minimizing shadows and reflections. Careful control of the ambient light environment is also essential.
Focus and Depth of Field
Maintaining sharp focus across the entire vial surface is another significant challenge. The lyophilized cake's surface texture and variations in fill levels contribute to focusing difficulties. This requires advanced imaging techniques such as:
- High-Resolution Cameras: Cameras with high resolution capture more detail, allowing for more accurate defect detection.
- Automated Focus Adjustment Techniques: Automated systems need to dynamically adjust focus based on the vial's content and position.
- Image Stitching Methods: For vials with a large surface area, image stitching techniques can combine multiple focused images into a single, high-resolution composite.
Background and Noise Reduction
Effective background subtraction and noise reduction are critical for accurate defect detection. Variations in vial-to-vial appearance and subtle background noise can interfere with algorithms designed to identify defects. Solutions include:
- Image Filtering Techniques: Various digital filtering methods can reduce noise and enhance image clarity.
- Advanced Algorithms for Noise Reduction: Sophisticated algorithms are needed to discriminate between actual defects and background noise, especially in low-contrast images.
- Impact of Vial-to-Vial Variations: Algorithms need to account for variations in vial color, transparency, and the appearance of the lyophilized cake.
Defect Detection and Classification Algorithms
The development of robust algorithms capable of accurately identifying a wide range of defects is a major challenge. Lyophilized vials can exhibit diverse defects, including: cracks, particulate matter, discoloration, and variations in cake morphology.
Developing Robust Algorithms
This requires sophisticated algorithms that can effectively differentiate between acceptable variations and actual defects. Key considerations include:
- Machine Learning Techniques: Convolutional Neural Networks (CNNs) and other machine learning techniques are increasingly used for defect detection and classification.
- Challenges in Training Data Acquisition: Obtaining sufficient and representative training data for diverse defect types is a major bottleneck.
- Handling Variations in Defect Appearance: Algorithms must be robust enough to handle variations in the size, shape, and appearance of defects.
False Positive and False Negative Rates
Minimizing both false positives (incorrectly identifying a defect) and false negatives (missing actual defects) is crucial. A high false positive rate leads to unnecessary rejection of good vials, reducing efficiency. A high false negative rate compromises product quality and patient safety.
- Algorithm Optimization Strategies: Careful optimization of algorithms is essential to balance precision and recall.
- Performance Metrics: Performance metrics such as precision, recall, and the F1-score are used to evaluate algorithm performance.
- Human-in-the-Loop Verification: In many cases, a human operator reviews the results to ensure accuracy and reduce the risk of false negatives.
Integration and Validation of Automated Systems
Integrating automated visual inspection systems into existing pharmaceutical manufacturing lines and ensuring regulatory compliance are substantial challenges.
System Integration with Existing Production Lines
Smooth integration requires careful consideration of several factors:
- Considerations for Throughput: The system must match the production line's throughput without creating bottlenecks.
- Compatibility with Existing Equipment: The system must be compatible with existing equipment and data systems.
- Data Management and Integration with Other Systems: Seamless data integration with Manufacturing Execution Systems (MES) and Laboratory Information Management Systems (LIMS) is critical.
Validation and Regulatory Compliance
Automated visual inspection systems must meet strict regulatory requirements to ensure their reliability and performance.
- 21 CFR Part 11 Compliance: Systems must comply with FDA regulations for electronic records and signatures.
- Performance Qualification (PQ): PQ demonstrates that the system consistently meets its performance specifications.
- Operation Qualification (OQ): OQ verifies that the system is installed and operates correctly.
- Installation Qualification (IQ): IQ confirms that the system is installed according to specifications.
Conclusion
Addressing the challenges in automated visual inspection of lyophilized vials requires a multi-faceted approach encompassing advanced image processing techniques, robust algorithms, and careful system integration. Successfully overcoming these challenges will lead to significant improvements in the efficiency and quality control of pharmaceutical manufacturing. Investing in innovative solutions and technologies designed to address these specific issues is crucial for advancing the capabilities of automated lyophilized vial inspection. Explore solutions for automated visual inspection systems for pharmaceuticals and automated lyophilized vial inspection to optimize your manufacturing process.
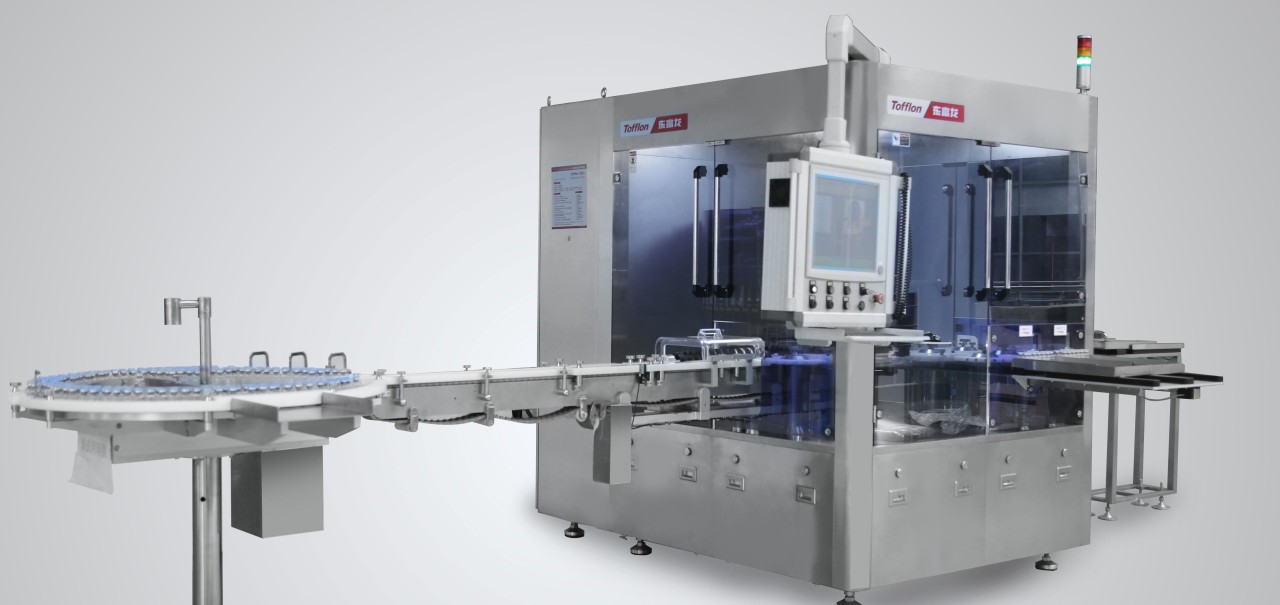
Featured Posts
-
Mlb Speedway Classic Manfred On Expected Fan Attendance At Bristol
May 11, 2025 -
Celtic Guard Payton Pritchard Contends For Nba Sixth Man Of The Year
May 11, 2025 -
Ai Powered Podcast Creation Analyzing And Transforming Scatological Data
May 11, 2025 -
Magic Johnsons Knicks Pistons Series Prediction
May 11, 2025 -
Como Abrir Una Cuenta Gratuita En Una Billetera Virtual Uruguaya Desde Argentina
May 11, 2025